- R&D Technology
- Product Development
-
- Forward R&D
- Possesses submount structure design capabilities: Combining thermodynamic simulation with COS closed-loop verification to establish a data model for submount structures and determine the optimal design solution.
- Ceramic material selection capability: By characterizing properties such as thermal conductivity, resistivity, and flexural strength, ceramics are screened to meet the specifications required for different application scenarios. The substrates include aluminum nitride, beryllium oxide, silicon carbide, and diamond.
- Process capability for various film layer structures: By performing actual measurements and thermodynamic simulations of film layer structures, microscopic morphology, and stress characteristics, the optimal solution is determined. Examples include Ti/Pt/Au, Ti/Cu, and W/Cu film layer structures, which can support a wide range of chip application scenarios for customers.
-
- Reverse engineering capability: Conducting DFMEA analysis based on customer application scenarios to identify key control points and perform corresponding design optimizations, enabling parallel substitution without altering customer usage habits.
- Innovative design capability: Building on reverse engineering, innovation is applied to improve and optimize the shortcomings of the original product, enhancing performance, reducing costs, or meeting other specific requirements.
- Prototype fabrication and testing capability: A fully in-house production line enables the rapid transformation of designs into physical prototypes, followed by rigorous testing to validate product performance and reliability.
- Reverse engineering R&D
- Seven Core Technologies
- Technical Capability
- Providing contract manufacturing services for various technologies.
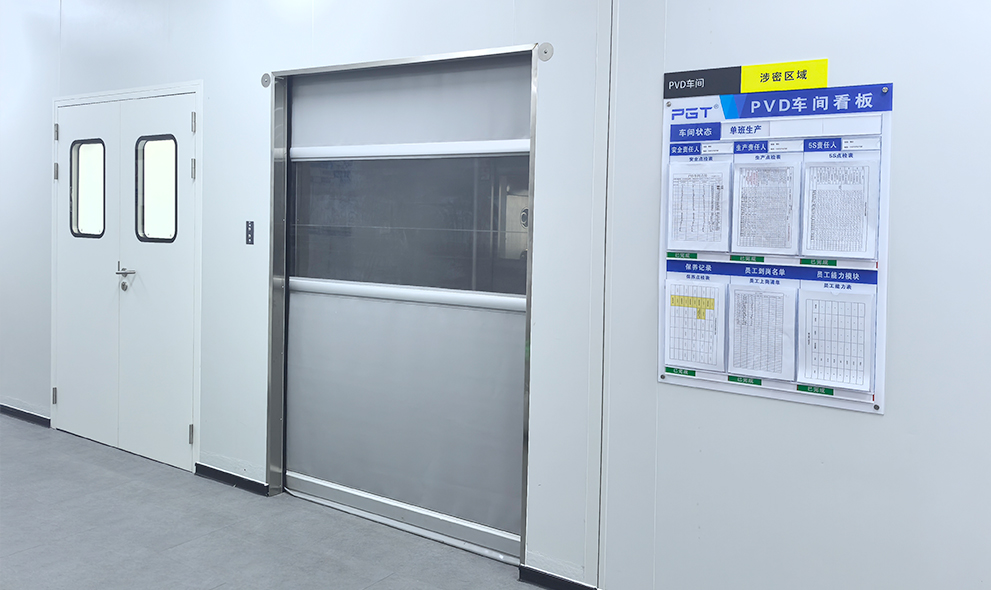
Using physical vapor deposition (PVD) to deposit a metal thin film on ceramic surfaces, enabling the welding of ceramics and metals:
1. Capable of depositing various metal film structures, such as Ti/Pt/Au, W/Cu, and Ti/Cu systems, etc;
2. Equipped to deposit metals on different substrates, including AlN, SiC, and BeO, etc;
3. Adaptable to various surface morphologies, supporting nanometer-scale roughness mirror-surface deposition.
PGT's ceramic metallization technology abandons traditional methods of physical surface roughening. Instead, it achieves chemical bonding between the metal and ceramic, resulting in higher structural reliability and stronger environmental tolerance.
1. Capable of depositing various metal film structures, such as Ti/Pt/Au, W/Cu, and Ti/Cu systems, etc;
2. Equipped to deposit metals on different substrates, including AlN, SiC, and BeO, etc;
3. Adaptable to various surface morphologies, supporting nanometer-scale roughness mirror-surface deposition.
PGT's ceramic metallization technology abandons traditional methods of physical surface roughening. Instead, it achieves chemical bonding between the metal and ceramic, resulting in higher structural reliability and stronger environmental tolerance.
- Ceramic Metallization Technology
- Photolithography
- DES Technology (Developing - Etching - Stripping)
- Thick Copper Electroplating Technology
- Planarization Technology
- Nickel Gold Electroplating Technology
- Pre-deposited AuSn Thin Film Technology
Material Characterization and Testing Platform
Production Process Inspection Platform
Laser Chip Bonding and Testing Platform
Collaborative Technology Resource Platform
- Inspection and Testing Platform/Capability
- Detection Capability
-
Characterize material properties through various physical and chemical measurement methods to support the design of the overall product structure.
- Measurement methods include:
- Thermal Analysis Characterization
- - Thermal conductivity measurement (thermal conductivity tester)
- - Coefficient of thermal expansion (TMA)
- Microstructure Morphology Characterization
- - SEM observation (EBSD analysis)
- - Step height measurement (profilometer)
- - 3D optical measurement
- Mechanical Performance Characterization
- - Flexural strength (universal testing machine)
- - Push-pull force testing
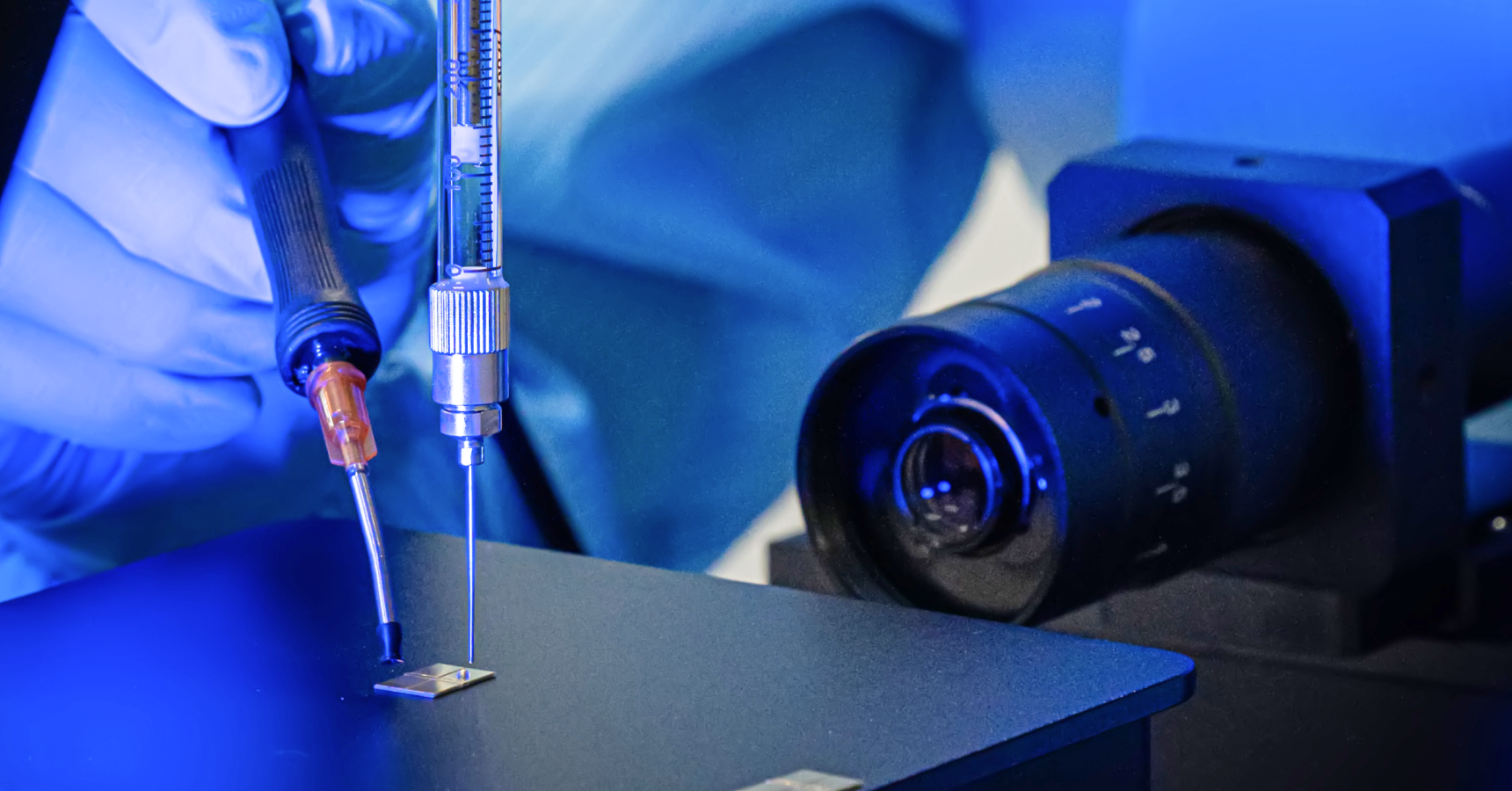
- PGT Laboratory
- COS Packaging and Testing Platform Laboratory
-
- High-precision eutectic bonding platform
- +/-3 um
Pulse heating
Pressure control
Nitrogen protection
-
- Wire Bond
- Industry-leading high-end welding equipment with high reliability for 1-mil gold wire bonding.
-
- Packaging Inspection
- Low/high magnification inspection, OH measurement, warpage measurement, push-pull testing, and other packaging reliability inspections.
-
- Push-pull force testing
- Temperature-stable control, covering multiple COS performance tests such as LIV, power, polarization, and wavelength.
-
- Failure analysis
- Internal and external product failure analysis, professional testing and analysis, 8D reporting, with industry-standard failure detection capabilities (e.g., dimensions, profiles, roughness, SEM, EDS, FIB, cross-section, X-ray, etc.).